Shrinking, curling and cracking can lead to problems with flooring. Using reinforcement may reduce their impact and lend greater strength to the floor.
Before we begin with this blog post, we need to be clear that there are many products, architect specifications and project related conditions that need to be considered and that you should always seek professional advice. Our intention here is to shed some light onto the topic and when we say “reinforcement” we do not mean “structural”.
The main purpose of reinforcement within screeds is to control shrinkage, curling, and cracking, which often appear during the process of drying, and give sub-floors extra toughness for greater resistance to impact. When a crack occurs, the reinforcement deflects the stress, slowing down crack propagation to minimise its width and spread. Screed reinforcement comes in two different forms: PP fibres and reinforcement mesh. Some screeding contractors may routinely use reinforcement in their jobs, unless there is a good reason not to.
PP Fibres
Polypropylene fibres, or PP fibres, are added to ensure that screeds will better support the stresses and micro cracking that can occur naturally during the drying period. Improving screed resistance to cracking, PP fibres prevent larger cracks from forming, minimising the danger of early screed failure. Evenly dispersed in screeds, PP fibres also increase screed resistance to abrasion and impact, whilst reducing problems at the surface along with the risk of delamination. Defined as the splitting of floor screeds into layers, delamination occurs when water and/or air is trapped inside screeds (e.g. when final floor finishes are installed before screeds dry optimally). PP fibres are usually used in bonded, unbonded, floating screed constructions and in screeds installed over underfloor heating pipes.
Reinforcement Mesh
Reinforcement mesh is used in cementitious screeds to deflect intrinsic stresses, which may lead to cracking during the drying stage, and in applications designed to endure heavy loads. According to BS 4483, D49 (and chicken wire in certain circumstances) can be applied to enhance the compression and flexural strength of screeds, increasing the bending moment (the point at which the screed bends as a result of external forces) and reducing the risk of shrinkage cracking around pipes and day joints. To lower the risk of cracking, a minimum width of reinforcement mesh is necessary and the screed should be laid at a minimum depth above the pipework, the details of which will require careful specification and are subject to product datasheets. Although D49 mesh is usually recommended to be placed at day joints, our experts prefer brick ties, which not only are easier to use but also deliver a solid, durable construction that can withstand a wide range of tensions and loads.
One or several cracks rarely compromise the integrity of a floor screed. In fact, a screeder can successfully apply a series of corrective measures to repair cracks and deliver a high-quality sub-floor, according to specifications. However, using reinforcement can help avoid time-consuming, costly repairs.
The type of reinforcement should always be selected according to type of screed, method of mixing, screed depth, and expected loads. Reinforcement is used in traditional and some modified screeds but not in anhydrite formulations. Though PP fibres and reinforcement mesh can be used in a wide variety of applications, they cannot replace structural steel. In this case, recommendation from the structural engineer or architect is necessary.
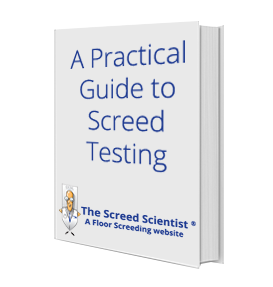
WHY SCREED TESTING CAN SAVE YOUR PROJECT TIME AND MONEY?
Download your free Practical Guide to Screed Testing here.